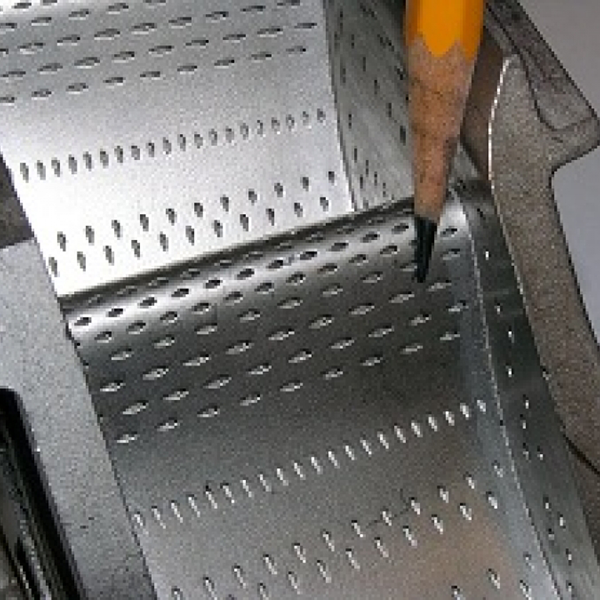
ファイバレーザーによる穴あけ加工
ファイバレーザーは、金属、コーティングされた金属、一部のセラミック、およびグラファイト複合材料への穴あけ加工が可能です。制御可能なエネルギー、ピークパワー、および時間プロファイル(または形状)など、穴あけ加工に適した機能を備えています。 ファイバレーザーを使用したレーザー穴あけ加工の鍵になるのはピークパワーです。また、TruPulse nanoシリーズは、材料との相互作用がピークパワー(最大20kW)とパルスエネルギーによって定義されるため、どちらのシリーズも穴あけ加工には最適です。
レーザー穴あけ加工における利点
レーザーによる穴あけは、ドリリングの市場の中でも最も有利に働くプロセスの1つです。当社のファイバレーザーシリーズは、高品質で、従来の方法では実現不可能であった正確で精密な穴を作成できます。
・非接触(摩耗や破損がなく、材料の歪みが最小限)
・非常に正確で一貫性のある結果
・入熱の正確な制御
・アスペクト比の高い微細な穴を作成する機能
・プログラミングの容易さと自動化への適応性
・セットアップ時間の短縮と使用する工具の削減による生産率の向上
・プロトタイプおよび小ロット製造の切り替えにおける柔軟性
・汎用性(同じツールをレーザー溶接とレーザー切断に使用できます)
・高度なビーム操作の能力(浅い角度および成形された穴を開ける能力を含む)
・複数の形状を一度に穴あけできる機能
・幅広い材料へのプロセスが可能
・金属への穴あけ
製造プロセスに合わせてさまざまな金属を適合させる必要性が高いアプリケーションがあります。上記で挙げたように、レーザー穴あけの最大の利点は、その適応性です。熱出力とビーム強度、およびパルス幅を正確に制御できます。これらにより、レーザー穴あけはステンレス鋼、銅、ニッケル、真ちゅう、鉄などのさまざまな金属で機能します。
金属以外の材料への適応性
製造プロセスに使用するものが金属ではない場合もあります。しかし、レーザー穴あけは、実質的にすべての金属で機能するだけでなく、半導体、プラスチック、セラミック、さらにはダイヤモンドなどの固体材料においても効果的です。さまざまな業界や使用する材料間における適応性、互換性を備えています。また、1台ですべてのプロセスが完結します。
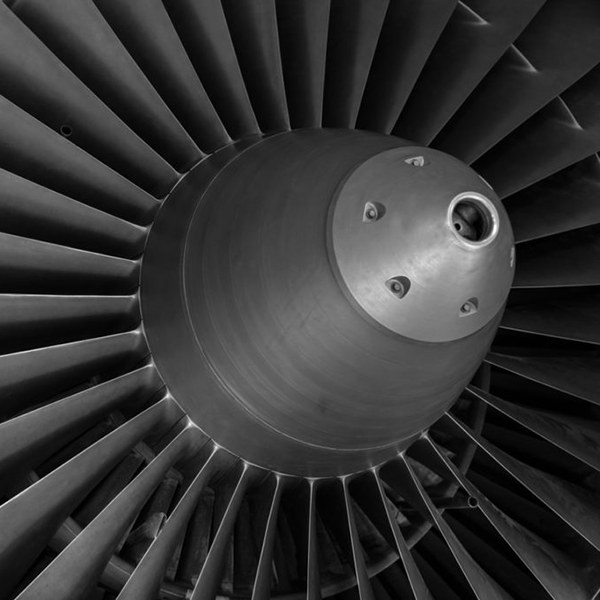
パーカッションレーザードリルとは
パーカッションレーザードリルとは、レーザーのフォーカススポットサイズを調整して穴のサイズを決定することを意味します。穴あけ加工中、レーザー光と部品の間に相対運動はありません。パラメータとパルス数は、高品質の穴を生成するように選択されます。この方法を使用すると、直径25µmから1000µmのレーザー穴あけが可能ですが、材料により範囲は異なります。パーカッションドリル技術で加工された穴は通常、直径300µm〜600µmの範囲にあります。
パーカッションドリルでは、「オンザフライ」と呼ばれる特別な穴あけ方式により、穴あけ速度を大幅に向上させることができます。オンザフライでの穴あけは通常、丸いタービンエンジンで実行され、モーションシステムエンコーダからの信号を使用して、部品の周囲の特定の一定間隔の穴の位置でレーザーをトリガーします。 穴をパーカッションドリルするために10個のパルスが必要な場合、オンザフライのシステムがパーツを10回転させ、1回転ごとに各穴の位置にレーザーパルスを送信します。サイクルタイムからインデックス作成時間が排除されるため、レーザー穴あけ速度が向上します。
パーカッションドリルは、パルス波形を利用して、レーザー光と材料との相互作用を改善することができます。これは、テーパーを制御し、穴あけ速度を向上させるのにも役立ちます。パルス波形は、レーザーのパルス幅をプログラミングしています。ロングパルスをオフタイムで区切り、短く分割することにより、穴の品質を向上させ、速度を上げることができます。穴から出てくる破片は、長時間のパルスの終了を妨げる可能性がありますが、分解すると効率が向上し、穴あけ時間が短縮されます。最初にピークパワーが低いパルス形状を使用すると、初期のベルマウステーパーが少ない穴を作成できます。
トレパンレーザードリルとは
トレパンレーザードリルでは、レーザーで穴を開けてから、パーツに対する光を動かして穴を「切り取る」ことができるモーションシステムが必要です。トレパニングにより、パーカッションドリルの約半分の直径公差が可能になります。多軸システムを使用して、調整されたテーパーで成形された穴を作成したり、深さで断面の変更などが可能です。
これには、優れた正確なモーション機能と高水準プログラミング機能を備えたシステムが必要です。トレパニングにより、特定の形状や大きな穴の切断、および大きな部品の複雑な3Dトリミングも可能になります。 金属に開けられた穴は、穴の直径の公差、テーパー、リキャストの厚さ、および微小亀裂によって判断されます。パーカッションドリル穴の穴の直径は一般に+/- 50µm未満であり、穿頭穴の公差は約+/- 25µmに厳しくなります。リキャストは、穴の内径の周りで再固化する溶融金属です。リキャストの厚さは合金と穴の深さによって異なりますが、通常は100µm未満です。穴の深さは50mmまで可能ではありますが、一般的に穴の深さは15mm未満です。
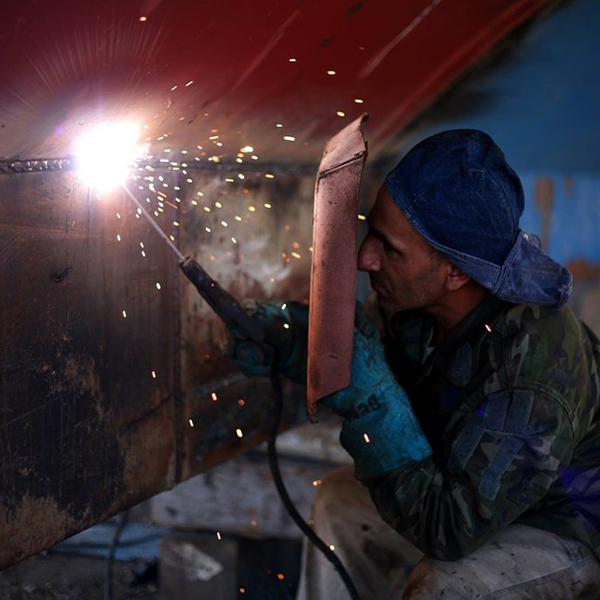
レーザー穴あけ加工が使用されている分野
製造業
レーザー穴あけは、多くの製造プロセスで広く使用されています。
自動車
自動車産業では、さまざまな複雑な部品の製造、製造、組み立てが必要です。この分野では、最終製品が安全で道路にふさわしいことが必要です。レーザー穴あけは、エンジンに燃料を供給するために使用される噴射ノズルに使用できる正確で精密な穴をすばやく作成が可能です。
航空宇宙
自動車産業と同様に、航空宇宙産業でも、複数の部品を安全かつ確実に製造および組み立てる同様のプロセスが必要です。この業界でのレーザー穴あけの一般的な用途は、飛行機のタービンエンジンに冷却穴を作成することです。
エレクトロニクス
レーザー穴あけは、エレクトロニクス産業で以前よりも有用になっています。この分野の専門家の技術者のたゆまない革新により、電子部品、オブジェクト、など、様々なものが小型化を続けており、微細な穴を機械的に開けることがますます困難になっています。レーザー穴あけは、この課題に対しても最適です。
医療
医療部門では、レーザー穴あけを使用して作成された多くの製品を使用しています。製品を安全に製造することが不可欠であり、レーザー穴あけによりこれが保証されます。この業界でのレーザー穴あけの用途は、デバイスに針穴を作成することです。
半導体
半導体業界でも、通常の機械では処理できない非常に小さく正確な穴を開ける必要があります。
レーザー穴あけの歴史
レーザー穴あけの歴史レーザーマーキング、レーザー彫刻、レーザークリーニング、そしてもちろんレーザードリルなど、当社のファイバレーザーシリーズは、さまざまなアプリケーションに対応します。1965年、Western Electric Engineering Research Centreによって製造されたレーザー切断機を使用して、ダイヤモンドに穴を開けました。それ以来、部品やオブジェクトの小型化により、レーザー穴あけはそれ自体が必要かつ不可欠なプロセスになっています。
まとめ
レーザー穴あけは大規模で複雑なプロセスであり、非常に多くの異なるアプリケーションに使用されるため、その可能性を完全に理解するのは難しい分野です。私たちは、よくある質問に答えるだけでなく、プロセスを分解するのに役立つ最も一般的なレーザー穴あけの用語を説明してきました。
また、レーザー穴あけのプロセスが、使用している金属に損傷を与えることなく正確にどのように機能するかについての詳細な説明については、レーザー穴あけの仕組みのページをご覧ください。 レーザー穴あけには様々なプロセスと用途、および技術があります。さまざまな材料に小さな穴を開けるだけでなく、多くのアプリケーションでの使用が可能です。製造業および生産産業で重要なプロセスになり、将来的ニーズも高まっていきます。